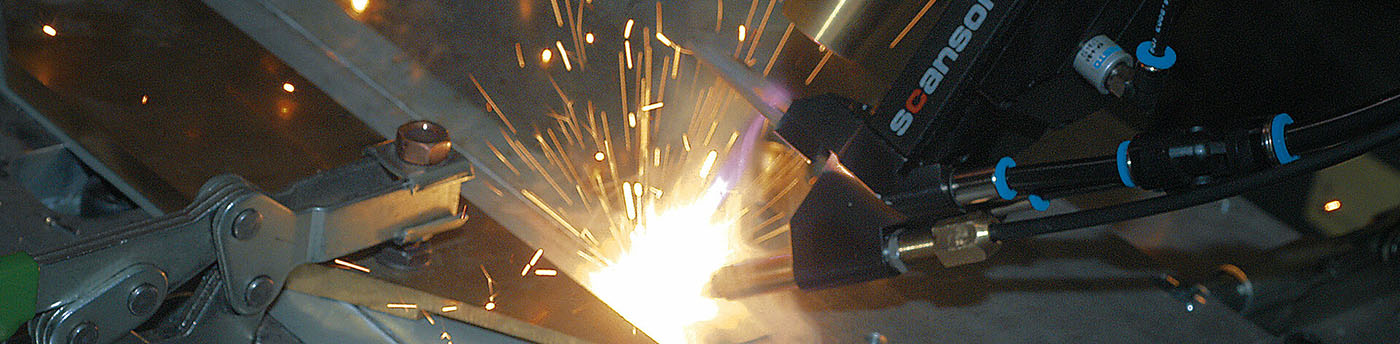
WELDING EQUIPMENT
Although soldering and welding are ancient techniques for joining metals, they are still ideally suited to modern, automated fabrication processes. Instead of the blacksmith’s hammer, contemporary industries use different methods such as laser beams for joining components.HT-GEAR drive systems ensure the highest precision and reliability in every welding or soldering process.
The oldest traces of welding techniques can be found in the Bronze age, more than 2.000 years ago, in boxed made out of gold. In the Iron Age, humankind learned to weld iron together and in the Middle Ages, blacksmiths still used a hammer. Modern welding was invented in the 19th century and has seen several innovations and new technologies. The latest is the introduction of laser into welding processes.
Laser beams can melt and even vaporize metals highly efficiently and very precisely. Joining thin sheets is therefore the domain of the laser. Whether soldering or welding, the seams are always extremely narrow, accurate and durable. The high energy applied at specific points allows impressive welding speeds. However, this performance requires high-precision control and positioning of the laser.
There are various processes available for automated soldering or welding. Whether soldering, induction brazing or laser welding – the weld filler metal is often delivered by wire. However, this is exactly where the difficulty lies. The system must always deliver a reproducible length of filler metal to the correct destination, but without jolting or bending the wire in the process. The automatic wire feeder driven by a controlled micromotor is another important application for our highly reliable drive systems.
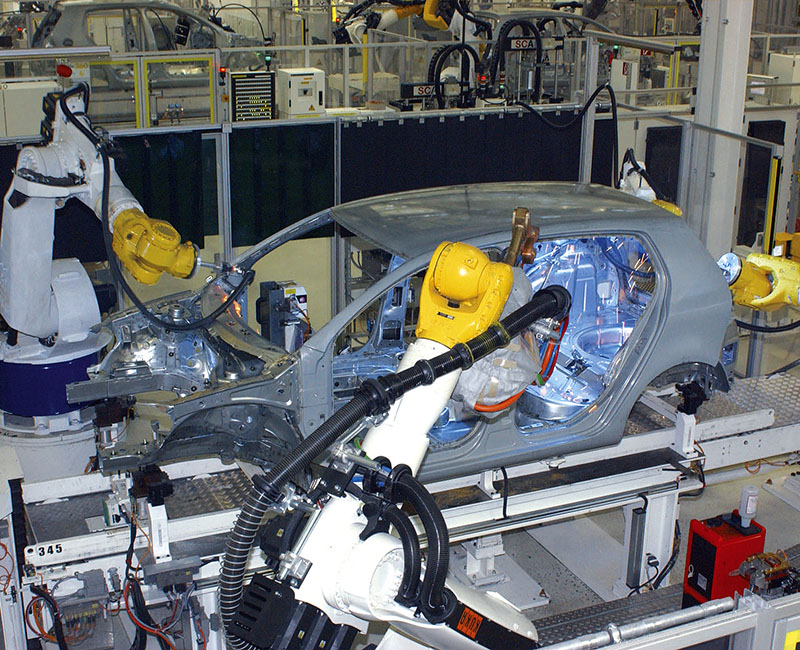
Regardless of whether it is our cost effective stepper motor, DC motor with high-resolution encoders or brushless motor for high dynamic positioning tasks – with the versatile and extensive HT-GEAR portfolio we strive to find the optimum drive solution that fits the needs of your welding application perfectly.

Highest precision and reliability

High dynamic positioning
